Was ist Operational Excellence?
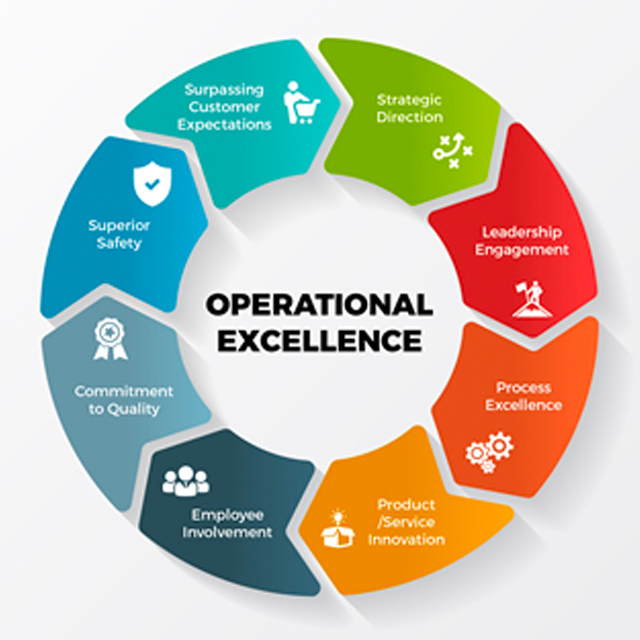
«Operational Excellence» steht für die kontinuierliche und dynamische Optimierung sämtlicher Prozesse und Systeme entlang der industriellen Wertschöpfungskette. Sie erfasst die Produktion und die Lieferkette, indem sie sich auf Anforderungen der Kunden fokussiert und – statt nur Symptome zu bekämpfen – Probleme an ihren Wurzeln anpackt. Entschieden und gehandelt wird ausschließlich auf Grundlage von Zahlen, Daten und Fakten, natürlich unter Berücksichtigung der Folgen aller Beschlüsse für das Gesamtunternehmen. «Operational Excellence» ist eine Investition in Mitarbeiter und Nachhaltigkeit. Dabei werden sämtliche Prozesse, Systeme und Strukturen kontinuierlich auf ihren Nutzen hinterfragt und optimiert. Das bekannteste Werkzeug der «Operational Excellence» ist Lean Production, entwickelt von Toyota in den 1950er-Jahren zur Optimierung der Produktion von Autos..
Nachstehend die «Lean Production-Definition des Instituts für Integrierte Produktion Hannover: Lean Production (auch Lean Manufacturing genannt) ist ein Teilbereich des Lean Managements und heißt übersetzt «schlanke Produktion». Lean Production bedeutet, dass Verschwendung vermieden und Produktionsfaktoren aus allen Unternehmensbereichen sparsam und effizient eingesetzt werden sollen. Produktionsfaktoren können sowohl Betriebsmittel, Personal, Werkstoffe als auch die Planung und Organisation von Unternehmensaktivitäten sein. Des Weiteren soll eine durchgängige und unkomplizierte Organisation und Verwaltung mit flachen Hierarchien geschaffen werden, weil dadurch Kosten gesenkt und die Produktivität gesteigert wird. «Lean Production» fokussiert sich dabei auf die drei Kernbereiche:
- Steigerung der Produktivität,
- Produktqualität, und
- Flexibilität/Agilität des Unternehmens und seiner Prozesse
Ein Schlüsselfaktor für eine zügige Erreichung der Stufe Operational Excellence sind heute Lean Automation und Digital Transformation. Dabei kommen die folgenden Methoden zum Einsatz:
Erklärung zu den «Low-Hanging-Fruit»-Methoden
5S bedeutet, salopp gesagt, aufräumen & putzen. Alle Materialien und Utensilien, die für die Produktion nicht notwendig sind, werden vom Arbeitsplatz entfernt. Die eingesetzten Werkzeuge werden mit sogenannten «Shadow Boards» (siehe das Bild mit Werkzeugen) geordnet, und sollen nach Gebrauch hier aufbewahrt werden. Ziel ist ein sauberer, und übersichtlicher Arbeitsplatz, an dem keine Zeit mit Suchen verlorengeht.
Kaizen steht für kontinuierliches Optimieren des Arbeitsflusses an der Produktionslinie. Unter Einbezug der Mitarbeiter prüft ein Team, wie optimal gearbeitet werden kann. Ein Beispiel: Prüfung der Laufwege mit dem «Spaghetti-Diagramm». Veränderungen werden umgesetzt und anschließend getestet. Mit kontinuierlicher Verbesserung der Prozesse (kurz: KVP) werden Arbeitsabläufe immer weiter verfeinert. Das kann sowohl die Linienaufstellung betreffen, aber auch bedeuten, dass die Regale mit Produktionsmaterialien am richtigen Ort platziert werden, um lange Arbeitswege zu vermeiden. Mittels KVP werden im Weitern Arbeitsplätze ergonomisch und sicher gestaltet mit dem Ziel, unfall- und krankheitsbedingte Abwesenheiten zu vermeiden.
Kanban bedeutet, alle Materialien, die zur Herstellung eines Produkts benötigt werden, sind am Arbeitsplatz verfügbar und werden und immer «automatisch» nachgefüllt. Diese Automatik kann mit verschiedenen Methoden garantiert werden, z.B. mit einem Kanban, das vom Lieferanten bewirtschaftet wird oder einer sogenannten «Milkrunner-Bevorratung» bei der interne Logistikmitarbeiter für die fortwährende Bestückung der Produktionslinie zuständig sind.
TPM steht für die Wartung der Produktionsanlagen während Stillstandszeiten (z.B. beim Umrüsten), um Störungen und Verzögerungen vorzubeugen. Produktionsmitarbeiter werden bei TPM aktiv in die täglichen (einfacheren) Wartungsarbeiten eingebunden. Der Unterhaltsdienst plant und führt komplexere Wartungen durch – jedoch bevorzugt außerhalb der Produktionszeiten. TPM verbessert die Planungssicherheit und kann die Betriebszeiten von Anlagen um bis zu 20% steigern.
Overall Equipment Efficiency (OEE), bei der Key Performance Indicators (KPIs) eingesetzt werden, ist eine wichtige Kennzahl für die Produktivitätsmessung. Es empfiehlt sich, für OEE ein einfaches automatisiertes Erfassungssystem für die Start- und Stopps der Produktionslinie zu installieren. Mit simplen digitalen Tools werden die resultierenden Daten analysiert. So werden die Ursachen von Stillstandszeiten sichtbar, und notwendige Maßnahmen können eingeleitet werden. Ursachen für Stillstandszeiten sind z.B. Warten auf Material, fehlendes Personal, unklarer Produktionsauftrag usw. Der Einsatz von «Lean Automation»- Systemen lohnt sich meistens innerhalb von wenigen Monaten.
Selbstverständlich gibt es zusätzliche Werkzeuge und Methoden, die – abhängig vom Projektstatus – weitere Verbesserungen bringen.
Gerne unterstützen wir Sie bei der Erarbeitung einer (Einführungs-)Strategie, bei der Auswahl der Methoden und ihrer Umsetzung. Anhand von Business Cases (Interim Management Operations), erfahren Sie, wie Lean Production/Lean Automation Ihr Unternehmen in kurzer Zeit weiterbringt.